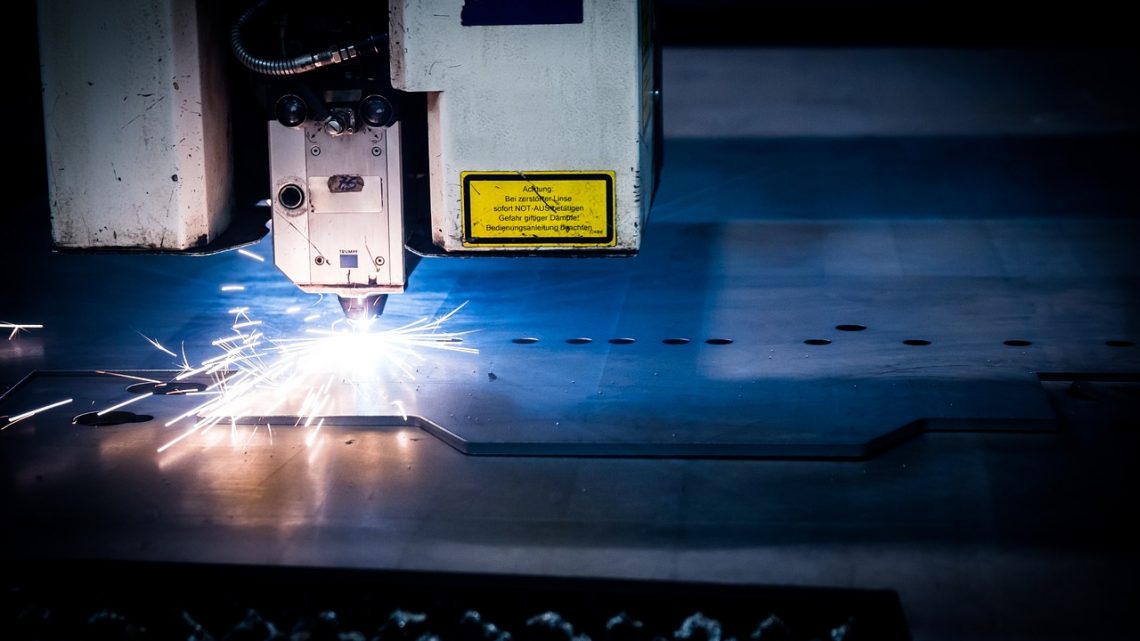
Vorteile & Nachteile des Wasserstrahl- & Laserschmelzenschneidens
Januar 7, 2023Der Zweck dieses Ratgebers ist es, einen Überblick über die Verfahren des Laserschmelzschneidens und des Wasserstrahlschneidens zu geben und die Unterschiede und Gemeinsamkeiten der beiden Verfahren aufzuzeigen. Zudem werden die Anwendungsbereiche und Vor- und Nachteile der beiden Verfahren dargestellt, um den Leser bei der Entscheidung für das geeignete Verfahren zu unterstützen.
- Einleitung
- Unterschiede zwischen Laserschmelzschneiden und Wasserstrahlschneiden
- Anwendungsbereiche von Laserschmelzschneiden
- Anwendungsbereiche von Wasserstrahlschneiden
- Vor- und Nachteile von Laserschmelzschneiden
- Vor- und Nachteile von Wasserstrahlschneiden
- Vergleich von Laserschmelzschneiden und Wasserstrahlschneiden
- Fazit
Unterschiede zwischen Laserschmelzschneiden und Wasserstrahlschneiden
Laserschmelzschneiden ist ein industrielles Schneidverfahren, bei dem ein Laserstrahl zur Bearbeitung von Materialien verwendet wird. Durch die hohe Energie des Laserstrahls können Materialien, wie zum Beispiel Stahl, Aluminium oder Kunststoff, geschmolzen und danach ausgeschnitten werden. Das Laserschmelzschneiden ist besonders präzise und kann auch komplexe Formen und Strukturen schneiden.
Wasserstrahlschneiden ist ein industrielles Schneidverfahren, bei dem ein hochdruckreiner Wasserstrahl zur Bearbeitung von Materialien verwendet wird. Durch den hohen Druck des Wasserstrahls werden Materialien wie Stahl, Aluminium, Stein oder Kunststoff geschnitten. Die Schnittgenauigkeit und -qualität kann je nach Material unterschiedlich sein.
Ein wichtiger Unterschied zwischen den beiden Verfahren ist die Art des Schneidwerkzeugs: Während beim Laserschmelzschneiden ein Laserstrahl verwendet wird, wird beim Wasserstrahlschneiden ein Wasserstrahl eingesetzt. Dies hat Auswirkungen auf die Materialien, die bearbeitet werden können und die Schnittqualität. Ein weiterer Unterschied ist die Schnittgeschwindigkeit: Laserschmelzschneiden ist in der Regel schneller als Wasserstrahlschneiden.
Anwendungsbereiche von Laserschmelzschneiden
Laserschmelzschneiden wird in vielen Industriebereichen eingesetzt, insbesondere in der Metallverarbeitung und -fertigung. Es ist ein sehr präzises Verfahren, das komplexe Formen und Strukturen schneiden kann. Zudem ist es möglich, verschiedene Materialien mit dem Laserstrahl zu schneiden, wie Stahl, Aluminium, Edelstahl, Kupfer und viele Kunststoffe.
Ein Vorteil von Laserschmelzschneiden ist die hohe Schnittgenauigkeit und -qualität, die durch den Laserstrahl erreicht wird. Zudem ist das Verfahren sehr schnell und kann daher auch für größere Mengen an Materialien eingesetzt werden. Allerdings gibt es auch Nachteile: So sind die Betriebskosten von Laserschmelzschneidanlagen im Vergleich zu anderen Schneidverfahren in der Regel höher. Auch die Umweltauswirkungen, wie zum Beispiel der Energieverbrauch und die Abgase, sind beim Laserschmelzschneiden höher als bei anderen Verfahren.
Anwendungsbereiche von Wasserstrahlschneiden
Wasserstrahlschneiden wird ebenfalls in vielen Industriebereichen eingesetzt, zum Beispiel in der Metallverarbeitung, der Steinbearbeitung und der Kunststoffverarbeitung. Ein Vorteil von Wasserstrahlschneiden ist, dass es für eine Vielzahl von Materialien einsetzbar ist, wie Stahl, Aluminium, Stein, Keramik und Kunststoffe. Zudem ist das Verfahren sehr sauber und umweltfreundlich, da keine giftigen Dämpfe oder Abgase entstehen.
Ein Nachteil von Wasserstrahlschneiden ist jedoch die geringere Schnittgenauigkeit und -qualität im Vergleich zu Laserschmelzschneiden. Auch die Schnittgeschwindigkeit ist in der Regel geringer. Allerdings sind die Betriebskosten von Wasserstrahlschneidanlagen im Vergleich zu Laserschmelzschneidanlagen in der Regel günstiger.
Vor- und Nachteile von Laserschmelzschneiden
- Schnittgenauigkeit und -qualität: Laserschmelzschneiden bietet eine hohe Schnittgenauigkeit und -qualität, die durch den Laserstrahl erreicht wird.
- Schnittgeschwindigkeit: Laserschmelzschneiden ist ein sehr schnelles Verfahren und eignet sich daher besonders für größere Mengen an Materialien.
- Betriebskosten und Wirtschaftlichkeit: Die Betriebskosten von Laserschmelzschneidanlagen sind im Vergleich zu anderen Schneidverfahren in der Regel höher. Allerdings kann das Verfahren aufgrund der hohen Schnittgeschwindigkeit wirtschaftlich sein, wenn größere Mengen an Materialien bearbeitet werden müssen.
- Umweltauswirkungen: Die Umweltauswirkungen von Laserschmelzschneiden, wie der Energieverbrauch und die Abgase, sind im Vergleich zu anderen Verfahren höher.
- Vor- und Nachteile im Vergleich zu anderen Schneidverfahren: Im Vergleich zu anderen Verfahren, wie zum Beispiel dem Plasmaschneiden, bietet das Laserschmelzschneiden eine höhere Schnittgenauigkeit und -qualität. Allerdings sind die Betriebskosten und die Umweltauswirkungen höher.
Vor- und Nachteile von Wasserstrahlschneiden
- Schnittgenauigkeit und -qualität: Wasserstrahlschneiden bietet eine geringere Schnittgenauigkeit und -qualität im Vergleich zu Laserschmelzschneiden. Die Qualität ist jedoch abhängig vom verwendeten Material und kann bei manchen Materialien höher sein.
- Schnittgeschwindigkeit: Wasserstrahlschneiden ist in der Regel langsamer als Laserschmelzschneiden.
- Betriebskosten und Wirtschaftlichkeit: Die Betriebskosten von Wasserstrahlschneidanlagen sind im Vergleich zu Laserschmelzschneidanlagen in der Regel günstiger. Allerdings kann das Verfahren aufgrund der geringeren Schnittgeschwindigkeit weniger wirtschaftlich sein, wenn größere Mengen an Materialien bearbeitet werden müssen.
- Umweltauswirkungen: Die Umweltauswirkungen von Wasserstrahlschneiden sind im Vergleich zu Laserschmelzschneiden geringer. Es entstehen keine giftigen Dämpfe oder Abgase und der Energieverbrauch ist niedriger.
- Vor- und Nachteile im Vergleich zu anderen Schneidverfahren: Im Vergleich zu anderen Verfahren, wie zum Beispiel dem Sägen, bietet das Wasserstrahlschneiden eine höhere Schnittgeschwindigkeit und eine größere Materialvielfalt. Allerdings ist die Schnittgenauigkeit und -qualität geringer.
Vergleich von Laserschmelzschneiden und Wasserstrahlschneiden
- Unterschiede und Gemeinsamkeiten: Laserschmelzschneiden und Wasserstrahlschneiden unterscheiden sich vor allem in Bezug auf das Schneidwerkzeug (Laserstrahl oder Wasserstrahl), die Schnittgenauigkeit und -qualität, die Schnittgeschwindigkeit und die Betriebskosten. Beide Verfahren können jedoch für die Bearbeitung von verschiedenen Materialien eingesetzt werden.
- Vor- und Nachteile im Vergleich: Im Vergleich zu Laserschmelzschneiden bietet Wasserstrahlschneiden eine geringere Schnittgenauigkeit und -qualität, ist aber günstiger und hat geringere Umweltauswirkungen. Im Vergleich zu Wasserstrahlschneiden bietet Laserschmelzschneiden eine höhere Schnittgenauigkeit und -qualität, ist aber teurer und hat höhere Umweltauswirkungen.
- Welches Verfahren ist das geeignete? Welches Verfahren das geeignete ist, hängt von den Anforderungen und Vorlieben des Anwenders ab. Wichtig ist es, sich im Vorfeld gut über beide Verfahren zu informieren und die Vor- und Nachteile abzuwägen, um das geeignete Verfahren für den jeweiligen Einsatzbereich zu wählen.
Fazit
Laserschmelzschneiden und Wasserstrahlschneiden sind zwei industrielle Schneidverfahren, die für die Bearbeitung von verschiedenen Materialien eingesetzt werden können. Sie unterscheiden sich vor allem in Bezug auf das Schneidwerkzeug (Laserstrahl oder Wasserstrahl), die Schnittgenauigkeit und -qualität, die Schnittgeschwindigkeit und die Betriebskosten.
Laserschmelzschneiden bietet eine hohe Schnittgenauigkeit und -qualität, ist aber auch mit höheren Betriebskosten und Umweltauswirkungen verbunden. Wasserstrahlschneiden ist günstiger, bietet aber eine geringere Schnittgenauigkeit und -qualität. Welches Verfahren das geeignete ist, hängt von den Anforderungen und Vorlieben des Anwenders ab.
Es ist wichtig, sich im Vorfeld gut über die beiden Verfahren zu informieren und die Vor- und Nachteile abzuwägen, um das geeignete Verfahren für den jeweiligen Einsatzbereich zu wählen